Machine Tools Segment
High-performance machine for users created by users who know all their needs
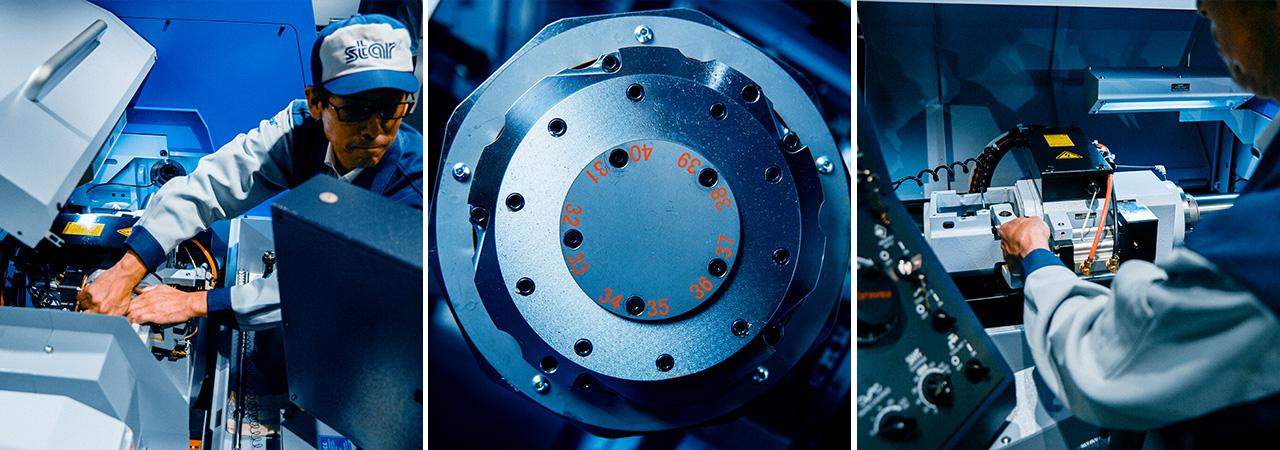
The history of Star Micronics' machine tool manufacturing began when we built our own automatic lathe to process our own watch parts in-house. Since then, Star Micronics have continued to produce machines that meet the needs of the market based on our basic philosophy of “machines created by users, for users.”
Since we began exporting to the United Kingdom in 1962, Star Micronics' machines have been highly regarded by users abroad as well as in Japan for their excellence and originality. Today, we have built a global network that includes production sites in China and Thailand, as well as sales offices spread across Europe, the United States, and Asia, and have established a support system for users around the world.
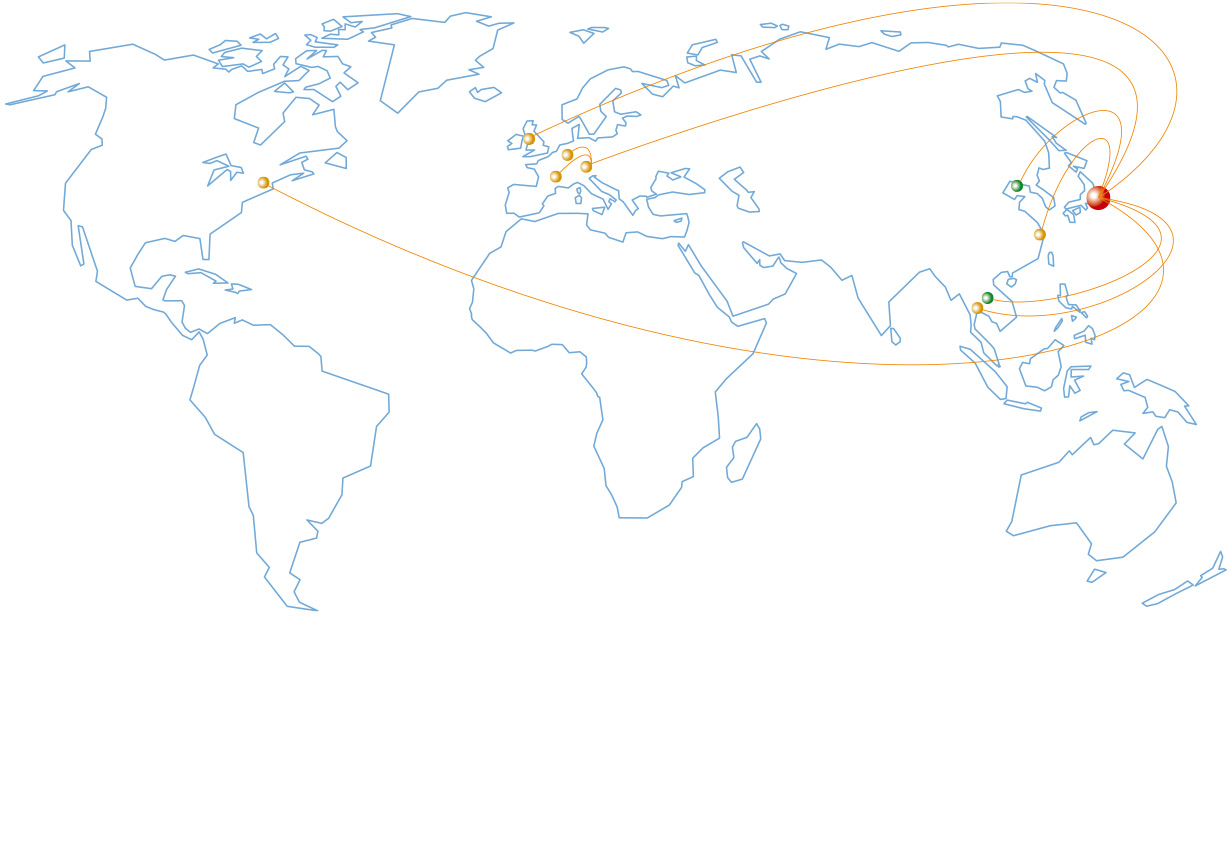
Star Micronics' Machine Tools for Producing Precision Parts with High Accuracy
Star Micronics' lineup of machines according to machining purpose.
From simple to complex machining, from small to large diameter, and from short to long material, we can fully cover all your parts machining needs.
Star Micronics' machine tools are mainly Swiss-type automatic lathes (also known as sliding headstock-type automatic lathe), which are suitable for machining small precision parts with high accuracy. The Swiss-type automatic lathe was originally invented in Switzerland in the 1870s as a machine for machining large quantities of watch parts.
When small-diameter parts, and long and thin parts are machined with a general-purpose lathe (Figure 2), the load generated during machining causes the material to deflect, making it impossible to finish to the correct dimensions. In the Swiss-type automatic lathe (Figure 1), a guide bush is used to stop the swing of the material, and the blade is positioned at a certain distance from the guide bush to process the material. As a result, even small-diameter parts, and long and thin parts can be machined with high precision without causing material deflection.
In recent years, the use of this technology has been expanding to all fields where high-precision small parts are required, such as automobiles, digital devices, and medical equipment.
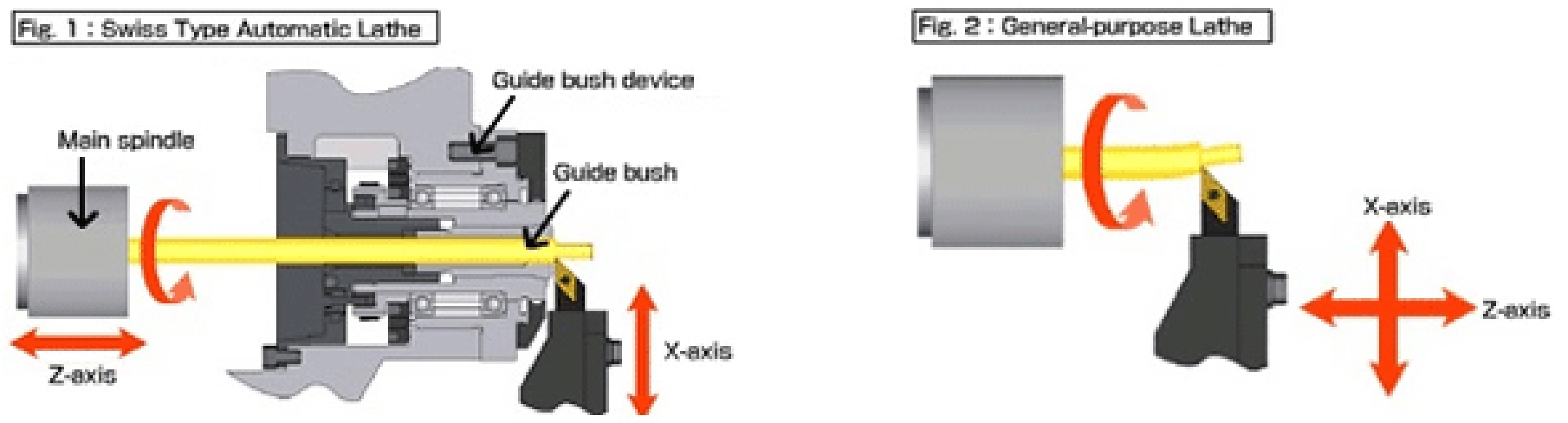
Star Micronics' unique technology supports precision parts processing
“Slanted dovetail slideway structure”
This is a sliding surface structure in which the base of the machine body and the tool post are inclined (slanted) and the sliding parts of both are processed into a trapezoidal shape called dovetail grooves to slide together. This structure allows the sliding parts to contact each other on the surface, improving mechanical rigidity. In addition, the center of the ball screw and the cutting point are close together, which reduces the load in the torsional direction (moment load) caused by cutting resistance.
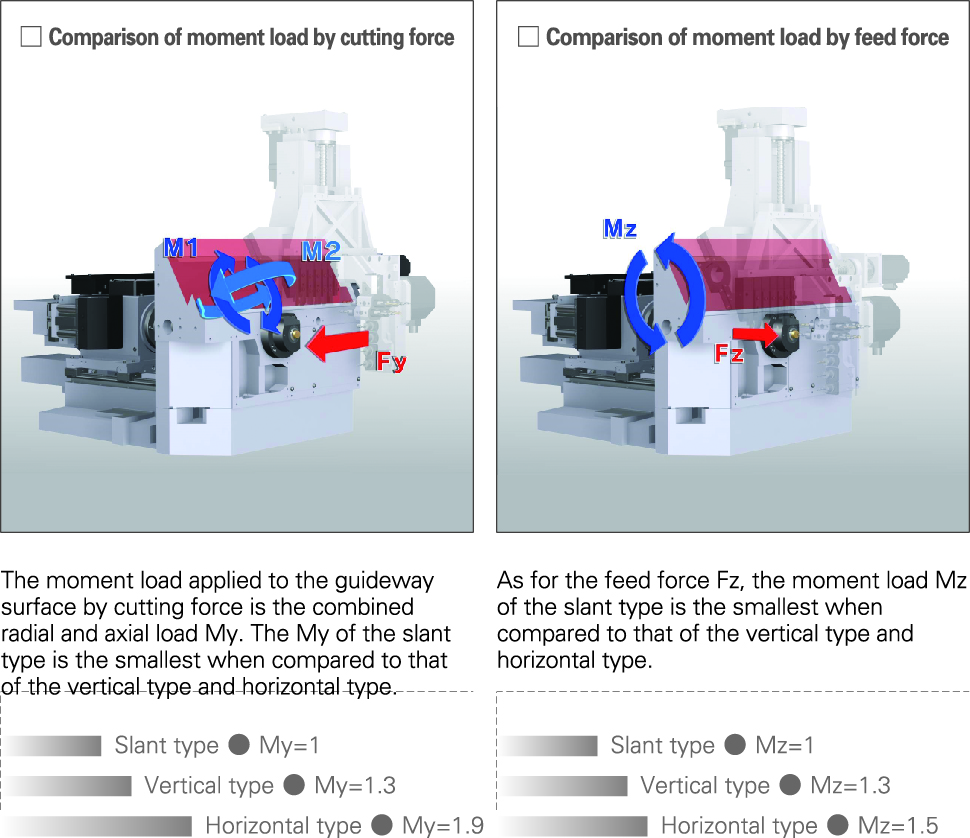
“Spindle Head Slide Guideway Structure”
To efficiently process parts with short overall length dimensions, the machine has been adopted for non-guide bush version with the guide bush device removed. This is a sliding surface structure with a guide ring machined to match the outer diameter of the main spindle cylinder of the headstock that moves while gripping the material. This structure, which eliminates the gap between the main spindle cylinder and the ring side guide surface, improves the rigidity of the headstock by supporting the machining load applied to the headstock during cutting on the sliding guide surface close to the cutting point.
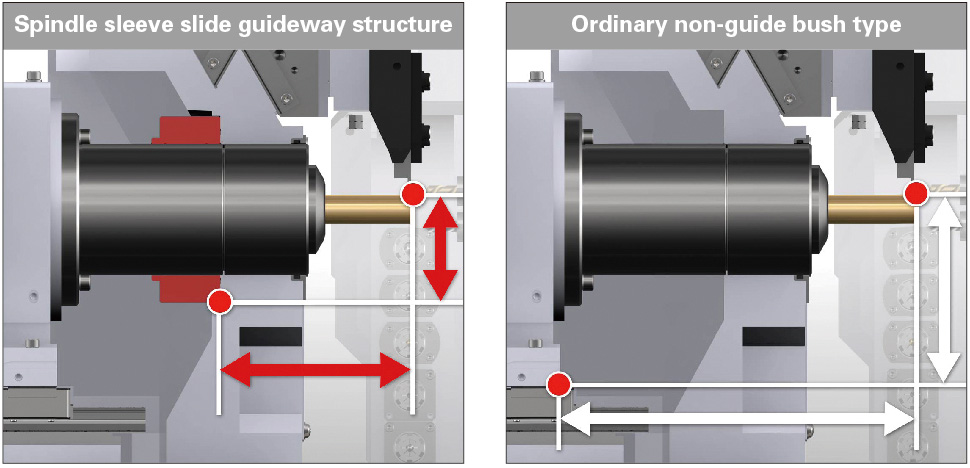
“Star Motion Control System”
This is Star Micronics' proprietary control technology developed to reduce cycle time and achieve efficient productivity. This control method reduces non-cutting time when parts are not machined by analyzing the NC program before operation and optimizing the switching time between control systems and tool selection operation. Because it is possible to control each axis in a slow motion without using the maximum speed during positioning operations, it is also effective in extending the life of consumable parts such as ball screws and bearings.
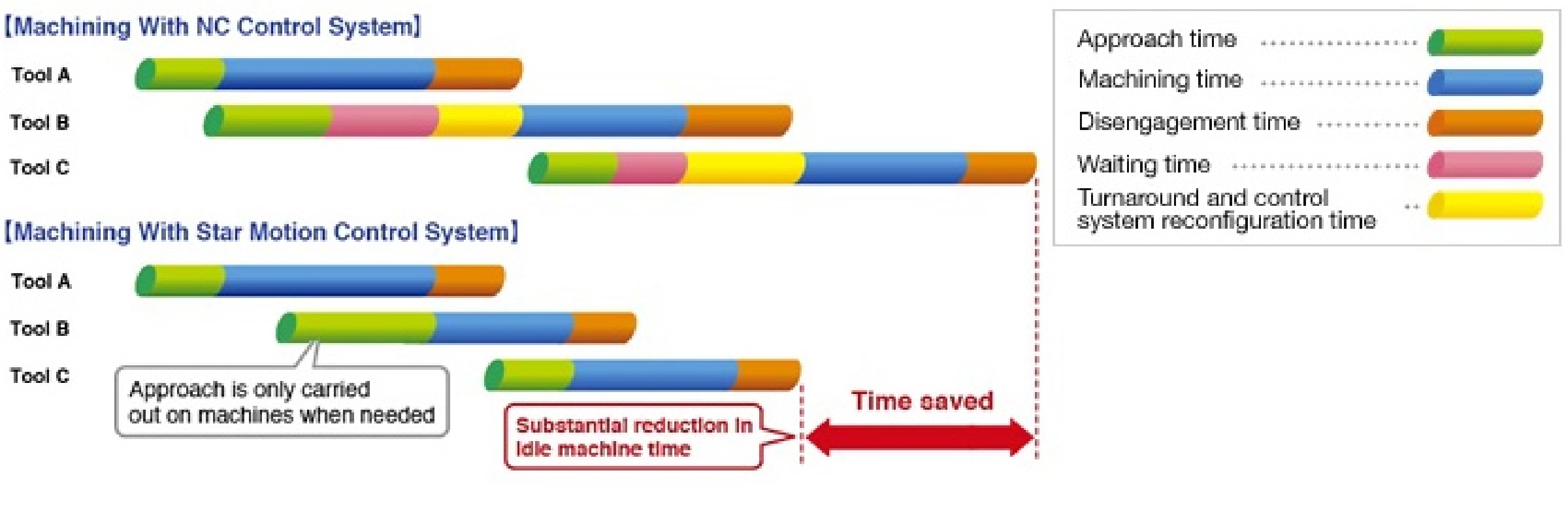